20th century technology cannot fulfill the needs of the 21st century supply chain. Replacing paper-based systems with modern technology is only a part of the solution. The main drivers of innovation for growth and profitability lie in redrawing operating models, unlocking liquidity, and reducing friction for customers.
However, supply chains are inherently complex. Until you can see through the maze of activities, you cannot redraw the new and efficient operating models (which sometimes hide in plain sight). Organizations cannot achieve the degree of sophistication required in new operating models to usher in a new era without supply chain visibility. And as McKinsey reports, “For companies in most sectors, a single prolonged shock to production could wipe out 30 to 50 percent of one year’s earnings before interest, taxes, and depreciation.”
What is supply chain visibility?
Supply chain visibility (SCV) is at the heart of everything a company does from tracking raw material quality and status to seeing where, when, how, and what customers buy (and return), SCV gives business more than just a look into the elements of their supply chain. It includes data about their entire business network, how they and partner organizations manage a list of activities and assets like finance agreements with partners; insurance coverage for risk involved in goods transit; supplier management, procurements, inventory, and logistics; production and sales motions, customer relationship management, and more.
Together, the activities form constellations across the value chain, making the supply chain so complex that it becomes challenging to manage everything as one body. Without supply chain visibility, the inefficiencies created by poor coordination of business activities across the value chain lead to waste, poor product quality, corruption, unfulfilled demand, increased inventory, and ultimately a weaker business position.
Examples of industries that depend on supply chain visibility
Supply chain visibility affects almost every industry. But, some are affected more than others. Some of the products most industries hit by global supply chain shortages include semiconductor manufacturing, automotive, industrials, retail, and x.
NOTE: Global supply chains are a maze. The maze spreads across industries, and some supply chain components, like semiconductor devices, affect multiple industries. The same is true for shipping and logistics, which are like a physical internet, and the cost of containers and shortage of containers affect multiple industries.
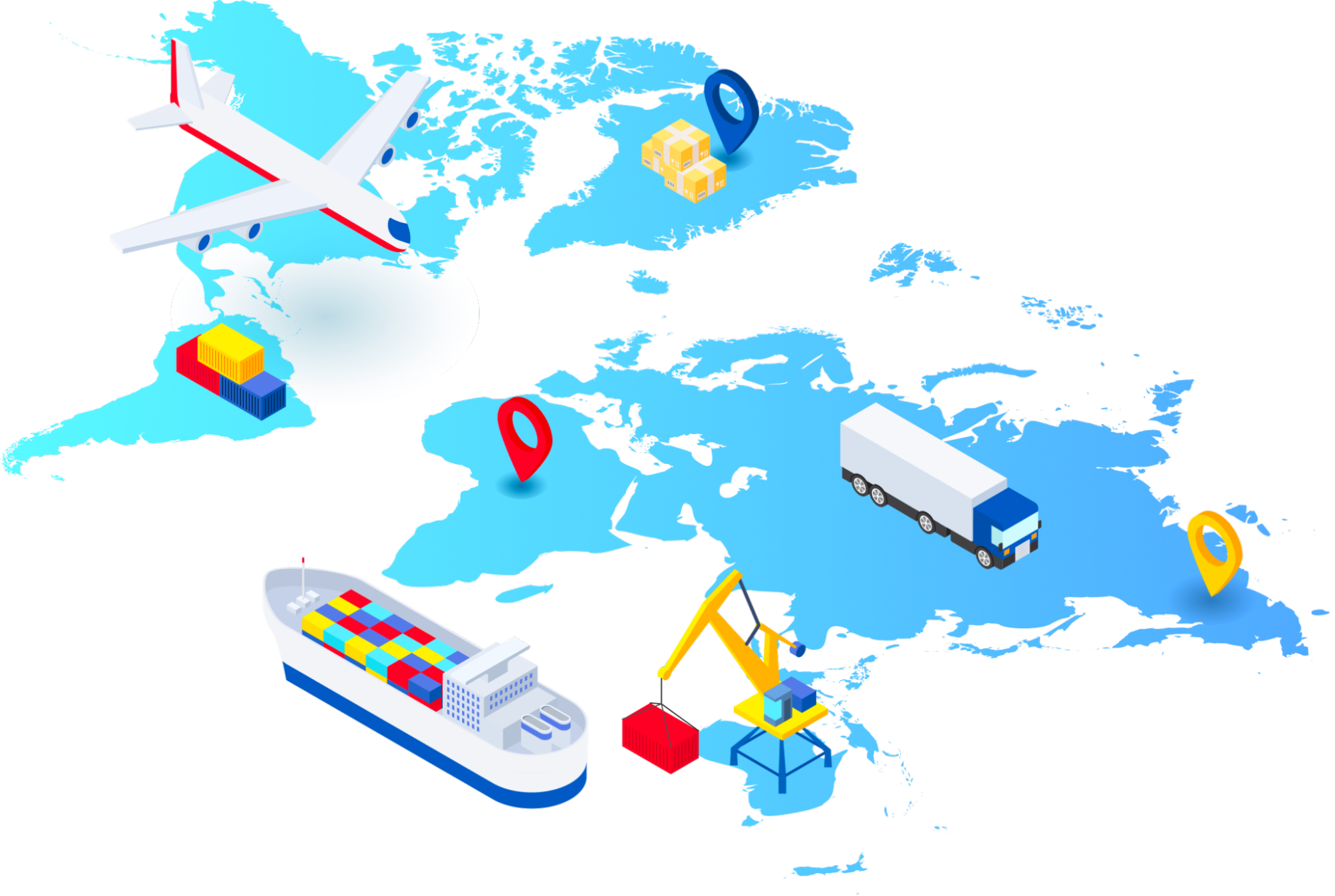
Supply chain visibility is a problem to solve with better partner collaboration through real-time data sharing across companies, clouds, and the entire value chain.
Semiconductors
In terms of products, semiconductors have been one of the most significant sources of global supply chain snarls, affecting a wide spectrum of industries. These include mobile phones, autos, and even lightbulbs. Computer and tech companies have been struggling to keep up with roaring demand that started when workers shifted to working from home. Coronavirus factory shutdowns slammed chipmakers’ (also known as foundries’) capacity to produce, leading to a sizable order backlog. Autos have been ground zero for semiconductor chip supply chain issues stemming from the pandemic. That has helped trigger a shortage of new cars and led to a massive spike in used car prices. While the demand and supply imbalance for commoditized chips is recovering, demand for premium chips that are used in autonomous vehicles and data centers is still surging.
Retail and ecommerce
Retailers have mixed exposure to supply chain disruptions, some have fared better than others. Key issues remain in the transportation of goods and labor. Large companies with local supply chains such as Bath & Body Works and William-Sonoma were protected from global shipping delays during the pandemic. But both large and smaller retailers are expected to struggle more when it comes to the cost of shipping goods: As Deloitte reveals, from January 2021 – August 2022, shipping costs rose by more than 77%.
To help improve inventory shortages, retailers have been starting to order products in advance, but the short-term gains have shifted into costly liabilities. Meanwhile, in the U.S., consumer economic health was in good enough shape that retailers were able to pass on the increased costs of higher inventory turnover times and shipping to consumers. But, in the face of inflation and other macroeconomic and market forces, it’s questionable how long those conditions will last.
Agriculture and food
Rising ingredient, labor, and utility costs because of supply chain disruptions have been pressuring companies in the food industry. The cost of common inputs for cooking, such as meat, wheat, and sunflower seeds used to make cooking oil, have skyrocketed as the Russia-Ukrainian War exacerbated supply chain disruptions. The price of wheat has risen 78% in the past year and more than doubled in the last three years. Corn and soybean prices are nearly double what they were three years ago.
The importance of supply chain visibility
The story of supply chain visibility doesn’t just end with excess inventory or inventory shortages. Depending on the industry segment, other challenges might include:
- Authentication of source materials
- Certification of end product integrity
- Validation of product conditions in transit
- Stakeholder distrust
- Transparency (or lack thereof) between stakeholders
- Outdated, ineffective, and high latency means of data sharing
- Regulatory compliance
A supply chain can be extraordinarily large, complex, and difficult to manage. With an end-to-end process that starts with design and materials sourcing, entails manufacturing, distribution, and logistics, and ends with sales, delivery, and support, a single product supply chain involves hundreds of stakeholders.
As if sheer size and scope of supply chain networks aren’t daunting enough, outdated or inadequate supply chain technology and legacy operations are a material drag on supply chain efficiency and transparency. Without better supply chain visibility, companies will struggle to spot shifting consumer tastes and expectations, improve demand management, provide visibility for the entire supply chain flow, trust one another to deliver as agreed, and track goods from raw material to end consumer.
There’s a quality story here, too. When established brands are not able to fulfill demand for goods and services, people look for alternatives, and you see all kinds of products enter the market. (I can confidently say from my experience buying hand sanitizers that half of them are not approved for use or consumption.) It leads to growth of counterfeit and contaminated products in the market. Supply chain visibility can give regulators a way to separate counterfeit and contaminated goods from genuine and fresh, better supporting the health of your population and mission-critical for national service. …Imagine counterfeit chips used in the satellite, defense and aerospace industry.
4 key benefits of supply chain visibility
Benefit No. 1 – Track products across the value chain
Companies can already track the components’ locations and quantities within their operations by using a radio-frequency identification (RFID) tag (on either the product or containers) and carefully placed scanning systems. While this type of tracking is helpful, it falls short of providing true end-to-end visibility.
To establish such visibility, all suppliers in a supply chain must combine their data in a single shared system and use a common standard for supply chain transactions.
- By sharing product location, time, and quantity data, manufacturers can automate and optimize end to-end processes across their business network.
- By tracking products and components in their supply chains, manufacturers can make sure they get the materials they need, when they need them.
- This visibility allows manufacturers to improve their production planning, reduce inventory levels, and react both faster and smarter to unexpected events impacting the supply chain.
Benefit No. 2 – Trace process conditions along the value chain
Generally, documentation is created by diverse stakeholders in the value chain; they apply different capabilities and use various systems and sensors. Typically, this means the manufacturer has a passive record of production conditions and characteristics at the end of a long communication chain. If a manufacturer discovers a bad batch at the end of this chain, it needs to work with all stakeholders to understand what caused the problem and cannot take action in time to switch suppliers.
In the food and pharmaceutical industry, manufacturers must prove safety and traceability to comply with stringent regulatory requirements.
- By sharing data on product and process conditions with next-gen blockchain, manufacturers can create a continuous digital product record of conditions under which product was transported.
- This will not only help in proving compliance, but partners can rapidly identify bad batches that should be eliminated.
Benefit No. 3 – Exchange digital product characteristics
Because records are kept by individual stakeholders along the value chain, in many cases, it is necessary to manually exchange records. Manufacturers must also conduct audits and quality checks to confirm that selected dimensions will meet the tolerances specified.
Creating a digital twin that follows the whole life cycle of the product, combining data on components, requires a high level of cooperation and coordination.
- By sharing and combining data, manufacturers can realize the full potential of digital twins. For example, a supplier can record the actual dimensions and geometries it is responsible for in the digital representation of the product.
- Suppliers responsible for subsequent process steps can seamlessly expand this model with actual dimensions and geometries that they have worked on.
Benefit No. 4 — Verify provenance
Unfortunately, in complex and heavily regulated supply chains, it is difficult to verify information through traditional methods, creating many opportunities for dishonesty and fraud. For high-value components or products, in particular, information regarding product origin or composition can be falsified, providing customers with a counterfeit component with lower quality characteristics than purchased. Another example is gray market diversion, with a supplier producing a higher volume of a specific component than requested and selling the excess units in a market other than the one originally intended.
- By sharing data, stakeholders along the value chain can create a continuous trail of records around this unique identification. With a tamper-proof trail, producers can then provide provenance and authenticity information as necessary by using this unique ID.
- The benefits are especially visible in industries that are heavily regulated and where fraud and counterfeiting can be costly and the origin of products are of particular interest.
Challenges for supply chain visibility
The problem of supply chain visibility is a problem of better collaboration across partners across the value chain. Three main collaboration models emerge:
- Between manufacturers through a third-party solution provider
- Between direct suppliers and manufacturers in a supply chain
- Between manufacturers through a machine supplier
Better collaboration is not possible without data sharing. In all these models, there are two main factors that motivate data sharing:
- Robust analytics for high performance – Manufacturers need sufficient data to further optimize production equipment. By sharing data and combining data sets, companies can form a data alliance and implement solutions they would not be able to realize alone.
- Increased transparency in value chains – Manufacturers increasingly need more visibility into products (including their origin, authenticity, location and condition) and production processes in the end-to-end value chain. They can gain this transparency by establishing tracking and monitoring systems, continuous digital records and process automation along the value chain.
But, two categories of challenges remain to be solved, trust-related barriers and technical barriers.
Trust-related barriers
- Fear of unintentionally giving away valuable or sensitive data about the business
- Fear of losing negotiation power or a competitive advantage
- Lack of visibility into data usage and analysis once shared
Technical barriers
- Risk of data breaches and losses
- Accessibility and interoperability issues that arise from combining data
- Different digital maturity levels among participants in the same solution
- Costs of switching technologies (or fear of technological lock-in)
How Vendia can help
During the last ten years, blockchain technology has promised a shared data ecosystem for supply chain partners. But too many of those first-generation blockchains — whether public or private — fell short of their potential. They lacked the enterprise readiness, scalability, and cloud compatibility required for success.
Next-gen blockchains, like Vendia Share, offer a way forward and overcome the problems and limitations of those early systems. These modern solutions are built for business use cases and meet the stringent enterprise requirements of the global supply chain:
- In a blockchain-enabled supply chain, itemized data related to products are collected in real-time, creating an immutable, instantaneous historical record with timestamps, locations, and conditions — from origin to consumer.
- With blockchain’s reliable identity and data management, all parties know not only who is participating in the supply chain, but which actions have been performed, at what time, and where.
- The immutable data record provides stakeholder visibility to the entire product flow, fomenting trust. From autonomous and self-executing smart contracts to blockchain-enabled document and process digitalization, blockchain reduces human touchpoints and eliminates the need for third-party intermediaries and local ledger reconciliation.
- All transactions are auditable, serving as a record of truth that can be easily accessed by regulatory bodies.
A layer of governance powered by blockchain technology will allow business networks to run on digital networks. The digital networks can supercharge current working relationships into trusted data alliances through provenance and transparency. Supply chain partners will unlock more value through economic interactions and networked activities, and organizations can prevent future crises such as those wrought with the global pandemic. Plus, organizations will have enough trustworthy data to see through supply chain inefficiencies and come up with new, innovative solutions to build new operating models for 21st century supply chains.
Blockchain for a modern data strategy
Learn how Vendia Share provides you with a next-gen blockchain platform that is optimized to solve supply chain visibility challenges and unlock new, significant market value without putting an additional IT burden on your existing IT workforce to manage and operate it.
Get the eBook, “Blockchain for a modern data strategy” or request a demo.